Plastic Molding
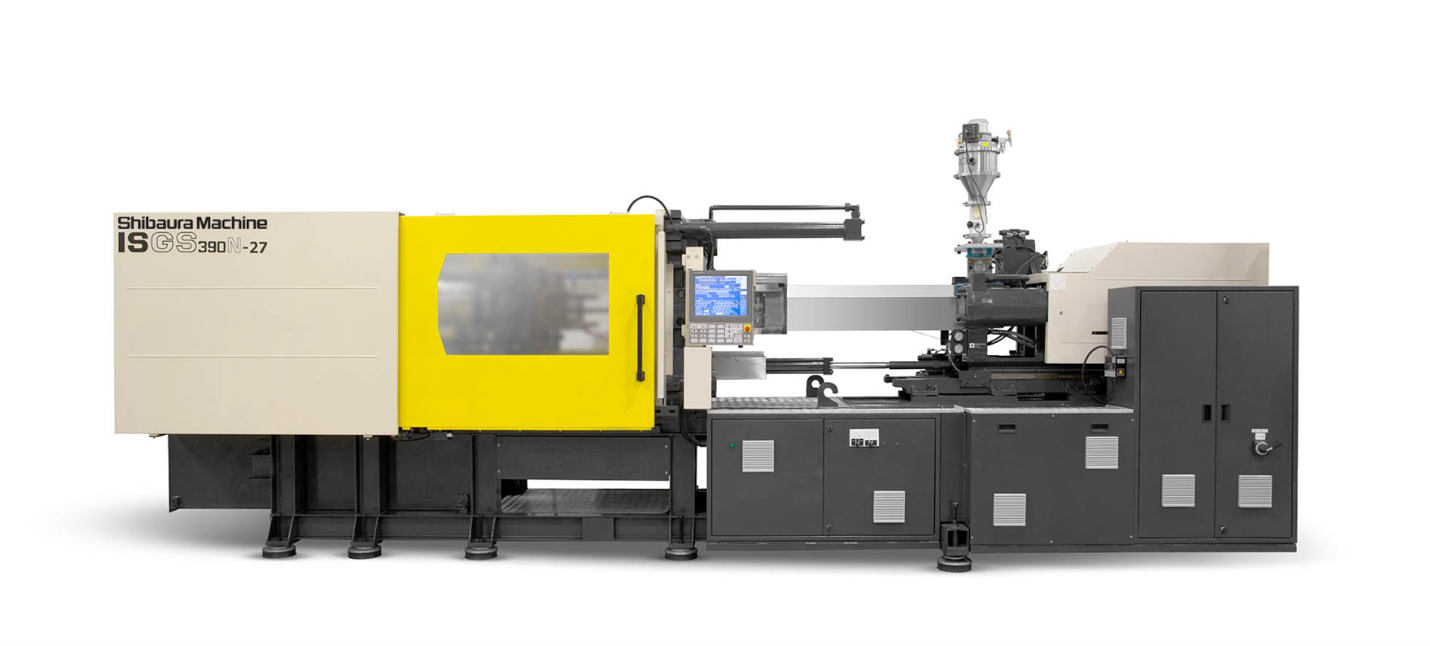
We have fifteen in-house plastic injection molding machines, 24/7 manufacturing on the molding floor. Be it short production runs to long production runs, we have the expertise and equipment to provide our clients with timely, cost-effective production using different materials.
The biggest challenge in injection molding is the process of designing a mold. There are almost no limits to our creativity but you can do the designs in clever and less clever way from a manufacturing point of view. We highlight this aspect as the most crucial part of injection molding. There will be no successful plastic part designs for injection molding if there is no perfect mold from where it is formed. The biggest factors to designing a mold are part and tool design. Getting these factors right means faster production, better quality and reduced costs.
Our product development process allows you to see your product designed, prototyped, and manufactured with every detail of the process in mind. We pride ourselves on how our team doesn’t specialize in or target one specific process or try to shoe-horn your product to fit a particular technique. As long as we can create the best product possible, we will use any method of product design and manufacturing necessary to see your vision come to life.
Be it an idea that needs a shape or moldable part that needs a final drawing, We can help 3D model almost any part through the very sophisticated software and expert CAD designers.
If you have an idea in mind and want to see how could it look or you need a prototype before the production, All is possible with our 3D prints through SLA Sterelithography, FDM or Jet 3D printing.
We have a In-House Full-Service Toolroom. We injection mold tooling solutions with specialization in production tool design along with comprehensive maintenance, repairs, and revisions of existing tools that ensure the life of our customers’ tools. Our engineers and mold builders produce injection molds that provide cavity-to-cavity consistency and repeatability by utilizing high-speed CNC mills.With the help of the CNC Machining, we machine both plastic and metal prototypes as well as aluminum or steel molds for plastic injection-molded parts. CNC machining is also used to produce steel or aluminum insert tooling for MUD frame systems.
Backed by rich engineering experience and manufacturing expertise, our time tested and proven systems continue to set the standards for injection molding industry. When production, precision and price are paramount, we will be your best choice. Our Engineers believe in Systematic Automation machines and robots . There are no electrical components to go obsolete or burnout, the entire system is pneumatic. The machine is designed with the operator in mind for maximum simplicity. Designed to grow your business, our Automation offers literally hundreds of attachment combinations to accommodate future applications. It could be robots or secondary operations; it could be robots used to take parts out of a mold; or it could be robots to put inserts or substrates into a mold when it comes to insert molding. Automation also has applications for your welded parts and assemblies — putting things like O-rings on parts, machining parts, anything like that where you can use a robot or some sort of mechanical device to perform a task instead of a human. The big goal is to have consistent cycles, and also reduce cycles — typically automation can do things faster than people can, as well as more consistently.
We can serve as an extension of your company. The plastic injection molded parts need to have some form of decoration applied to them after being manufactured. Possible reasons for decorating or marking parts include identification, tracking, branding, notices, warnings, instructions, as a product attribute, or otherwise. There are some standard methods of decorating plastic parts, and each has certain advantages and considerations, depending on the part application, the decorating purpose, and the resin being used. Some of the services offered are In-Mold Labeling, Screen Printing, Hot Stamping, Heat transfer, Foil Printing, Pad Printing, Laser Marking, Decal Transfer, Die Cutting, Felt & Gasket Placement.
Packaging for products is almost as important as the product itself. That is why we have fine-tuned the packaging process so that all of our customers receive products ready to hit the shelves. We assist our customers in distribution; We work closely with our customers assessing both short- and long-term requirements. We will ensure that you have exactly what you need, right when you need it.